Metal Stamping


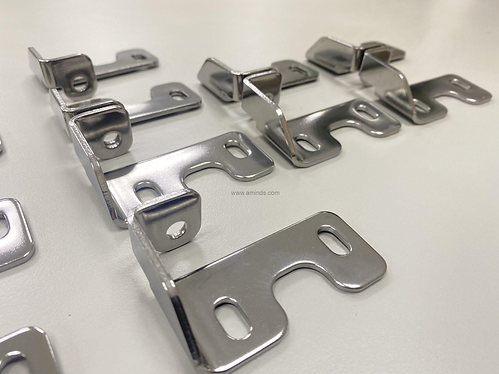
What is Metal Stamping ?
Metal stamping is a versatile and cost-effective manufacturing process that involves forming, shaping, or cutting metal sheets into various desired shapes and sizes. This precise and efficient technique utilizes a stamping press, which can employ a variety of dies and tooling to transform flat metal sheets into intricate components. Ideal for high-volume production, metal stamping is widely used in the automotive, electronics, aerospace, and appliance industries to create components such as brackets, panels, and connectors. The process offers advantages in terms of speed, repeatability, and the ability to maintain tight tolerances, making it a preferred method for producing intricate and consistent metal parts with efficiency and accuracy.
Benefits of Metal Stamping
-
Cost-Effective Production: Metal stamping is highly efficient for large-scale production, making it cost-effective due to its ability to rapidly create parts with minimal material waste.
-
High Precision and Tolerance: The process allows for the production of highly precise and complex metal components with tight tolerances, ensuring consistency and quality in the final products.
-
Speed and Efficiency: Metal stamping is a fast and efficient manufacturing method, enabling high-speed production of parts. This is crucial for meeting tight production schedules and demands.
-
Versatility: The versatility of metal stamping allows for the creation of a wide range of shapes and sizes, making it suitable for diverse industries and applications.
-
Material Utilization: Metal stamping optimizes material usage, reducing waste and contributing to sustainability efforts. This is particularly important for cost savings and environmental considerations.
-
Consistency and Reproducibility: Metal stamping ensures consistent and reproducible results, reducing variability in the production process and improving overall product quality.
-
Complex Geometry: The process can handle intricate designs and complex geometries, enabling the production of parts with detailed features that might be challenging or costly with other manufacturing methods.
-
High Production Volumes: Metal stamping is well-suited for high-volume production, making it an ideal choice for industries with large-scale manufacturing requirements.
-
Reduced Secondary Operations: Often, metal stamping produces parts with finished or near-finished surfaces, reducing the need for additional machining or finishing processes, thus saving time and costs.
-
Strength and Durability: Stamped metal parts typically exhibit high strength and durability, meeting the performance requirements of various applications, including those in demanding industries such as automotive and aerospace.
How we do it
-
Design and Tooling: The process begins with the creation of detailed designs for the desired metal components. Tooling, including dies and molds, is then fabricated based on these designs. The tooling is crucial for shaping and forming the metal sheets accurately.
-
Material Selection: The appropriate metal material is selected based on the specific requirements of the project. Commonly used materials include steel, aluminum, and stainless steel. The chosen material should possess the necessary properties for the intended application.
-
Feeding the Material: Flat metal sheets are loaded into the stamping press. The sheets can be in coil or sheet form, depending on the production requirements. Precision feeding mechanisms ensure accurate positioning of the metal sheets for stamping.
-
Stamping Process: The stamping press descends, and the tooling, including the dies, exerts pressure on the metal sheet. This pressure causes the material to deform and take the shape of the dies. Various operations can occur during this stage, including blanking (cutting the part from the sheet), bending, drawing, and coining.
-
Quality Control: Throughout the stamping process, quality control measures are implemented to ensure that each stamped part meets the specified tolerances and quality standards. Automated inspection systems or manual checks may be employed.
-
Secondary Operations (if necessary): Depending on the complexity of the part and customer requirements, additional secondary operations such as welding, machining, or surface finishing may be performed to achieve the final product specifications.
-
Cleaning and Finishing: Stamped parts may undergo cleaning processes to remove any residual oils, lubricants, or debris. Surface finishing techniques, such as painting, plating, or coating, can also be applied to enhance aesthetics and improve corrosion resistance.
-
Packaging and Shipping: The finished stamped components are carefully packaged to prevent damage during transportation. Proper labeling and documentation are prepared for accurate inventory tracking and shipping.